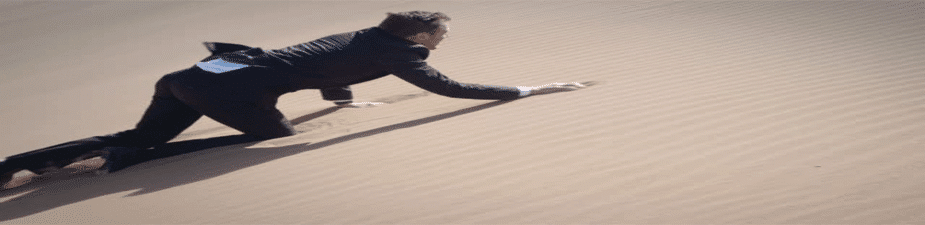
Is Your Safety System Really Just a Mirage?
You think it’s there and fit for purpose. Guess what? Probably not….
Measuring safety performance is a key performance indicator for almost all business today. There are many reasons for the focus. We might like to think it is because business is about making sure everybody goes home as well as when they arrived. Or we might like to think it is about promoting a competitive advantage.
Let us take a look at some of the available evidence.
The most commonly utilised safety measure, used almost universally throughout the global community, is the Lost Time Injury Frequency Rate (LTIFR). It has become a behemoth accepted by government and industry everywhere. You attend corporate safety conferences and people might as well be tattooing their LTIFR number on their forehead, the way it is often talked about. I often am gobsmacked at the collective ignorance within these rooms. Often these attendees are the “movers and shakers” with respect to safety, within their respective business units. It is scary how many have no idea as to the history of the metric, don’t know how it is calculated.
In Australia the Standard AS/NZS1885.1-1990 actually designates LTIFR as the statistic of choice.
This thinking was challenged at a workshop conducted by Dr Frank Rose, of ICI (UK), who, like myself, believes it to be fundamentally flawed. Frank stated:-
“I really passionately believe that people have the right, the unchallengeable right, to go to work and to work safely and to not have their health damaged. And so, its totally unacceptable for me to see organisations or governments that budget for a certain number of fatalities, a certain number of lost time accidents, a certain number of medical treatments and a certain number of illnesses. If we are in the business of promoting OHS, why do we use failures as the measure of our success?” (Rose, 1994)
It is very hard to argue against this view and yet we often do. Frank said it over thirty (30) years ago.
So let us explore how our followers actually manipulate LTIFR (maybe they do so thinking they’re protecting the leader or the business; that’s an important question for another day).
Here are a few examples I have either witnessed, or become aware of, in the last twelve months or so; there are many more although I am sure you shall see the point with these ones.
- The Site Safety Manager is in a Meeting and takes a phone call on his injury mobile phone (yes, a unique phone number for injury reporting direct to him). I overhear him saying to a colleague he has to get to a doctors surgery as an employee has just received a medical certificate advising time absent from work. He was going to the Surgery to have the certification changed. At this point the Site Safety Manager had no knowledge of the injury or indeed how severe it was. What do you think is going on here?
- The worker who has a fall and has severe pain in their right leg. There is swelling, clear discolouration and the workers pallor is white. This fall occurs around 1PM on a shift that is due to finish at 3:30PM. So what happens with this one? The Site Foreman goes up to the Worker and says they shall transport him to the Doctors’ at the end of shift. Says it only looks sprained and arranges for someone to keep an eye on him till end of shift. As it turns out this worker had a broken leg and layed on the lunchroom table for a few hours. You may have worked out for yourself this worker was also in shock.
Remember our Site Safety Manager who was driving the work ute (read Ferrari) to the Doctors Surgery. The standard spiel is “Doc; we are a progressive company who takes the health of our employees very seriously. We shall make whatever light duties available that are necessary”.
If the Doctor gives up we find another LTIFR input “saved” and the Site Safety Manager has “hit a winner”.
So what about this situation?
Conducting a safety culture assessment I am wandering about the Plant with my escort chatting to workers about their roles etc. One of the guys quietly suggests I check out the “crib hut” in Section X. Anyway I keep wandering and after I while I ask my escort can we go by Section X, so off we go. Fortunately he was unaware my objective was the “crib hut”. As we were looking at the scaffolds and talking to the riggers I asked that I have a look at the “crib hut”. My reason was that it seemed a bit “out of the way” and I wanted to ensure that it was not being used as a store for the riggers equipment and the welders gases. In we go and there’s four guys playing cards. As it turns out this is the “dead mans zone”. Those persons, for whom those often promised light duties cannot be found, get to spend their day reading magazines, playing cards etc. These people were not playing cards in “reception”, they were way out in the “back blocks”. What do you think is going on here?
Now you may be thinking these are unscrupulous employers. They were not. Each of these workplaces are highly regarded within their industries and are amongst some very large workplaces.
The biggest hole within LTIFR though, beyond these overt manipulations, is the fact that if a person is a rigger, has a fall, breaks their leg, lays in the lunch-room, gets to the Dr’s, has plaster applied, and then spends eight (8) weeks playing cards, we have no input to LTIFR. In other words none of this ever happened. Ouch!
Now the above description you might consider to be an extreme case of statistical manipulation. I suggest to you, the principle is alive and well. Whenever I conduct safety workshops, anywhere in the world, the same stories are told – just the names change?
Within LTIFR inputs, any worker who does not lose time is not included. So no wonder everyone is running around creating non-existent suitable duties. I would also put it to you that whilst “dead man zones” may not be so overt in your organisation; you probably have pockets of people doing jobs like collating, filing, checking, etc. In the safety trade we often refer to this as “stamp licking”.
There is an argument that LTIFR should be modified to define “lost time” as the time lost from your normal job. Sadly, it shall never happen, as there is too much politics and corporate investment in the maintenance of this regularly manipulated statistic. Major multi million dollar contracts are won and lost based upon reported LTIFR’s.
LTIFR is a reactive approach to safety that uses systems etc in finding a transient job for the injured worker. The “system” actually rewards organisations for using this process of hiding injuries.
Why don’t the Regulators financially reward organisations for implementing management systems and creative approaches to managing risks?
What incentive does an organisation have to implement management systems and control risks if they haven’t had high cost injuries to get the premiums up?
Or why don’t they look at the actual incident frequency rates?
As these real-world examples demonstrate; you can seriously injure a worker, have them back at work doing basically nothing and reduce your insurance premiums by using this approach. There has been little or no lost time but the injuries are substantial.
This approach does nothing to address the risk that caused the injury or illness in the first place, and actually gives the impression to employees they will be punished with some boring job if they report injuries. They would prefer to take a sickie or two so they keep the job they’ve worked their way to over the years.
Just to conclude this exploration. Explain to yourself how the lost time from a cut finger that has become infected (probably from licking those envelopes that are part of their light duties) has greater impact than the person who has broken their leg and may require multiple surgeries before they are “right”?
So what are your responsibilities as a Leader within the business. You may be reading this all smug saying this does not happen here. Well sorry! To some degree it probably does. In all of the examples provided, the Leader of the business was unaware what was happening (the provision of suitable duties excluded).
You really should be looking beyond the safety metrics and getting out there and making it clear to your followers what you expect and accept as safety leaders within the business.
Management by manipulation is unacceptable and fatally damages your safety culture.
Worth a thought?
To read the author’s Dodgy Didget’s article on Linkedin just Click Here.
To read more about the author of this article just Click Here.
“The psychological state of the human being plays a large role in how well they do their work.”
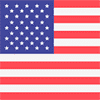
Ricky, Atlanta
“I was fortunate to attend Transformational Safety’s Anatomies of Disaster Program. This was amongst the most powerful two days I have ever spent in a room. From the outset David Broadbent set the scene by dedicating the program to the late Rick Rescorla – the man who is credited with saving over 2700 lives on 9/11. Throughout the two days David would often respectively reflect and remember those who had died, or been injured, in the disasters we explored. He would say, and I will never forget, “…we must always remember those that lost their lives lift us up into the light of understanding”. I learnt so much. HRO, Resilience Engineering, Critical Incident Stress Management (CISM) and more. Those of us who were there are still talking about it…… Thankyou David
