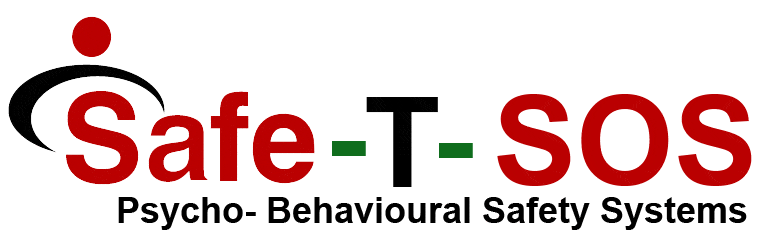
The SAFE-T-SCAN© Mini Risk Assessment
SAFE-T-SCAN
The SAFE-T-SCAN© Mini Risk Assessment is the next step in the behavioral chain of decision making. Whilst the SAFE-T-START© Card introduces the employee to an elemental consideration of the general requirements that they may confront within their work task, the SAFE-T-SCAN© takes that consideration to the next level.
The SAFE-T-SCAN© Mini Risk Assessment takes employees through a four (4) step process which culminates in a decision to either proceed with the task, proceed with the task following further education/equipment/PPE provision etc, or abandon the task – and seek an alternate methodology.
The four steps of the SAFE-T-SCAN© The SAFE-T-SCAN© four (4) step process leverages the seminal influence of Operational Risk Management (ORM); a key hazard management tool of many military organizations around the World. Remember military operations are the one workplace where your competitor is out to kill/maim you. Therefore the hazard and risk management approaches, by definition, need to have the ability to function within toxic work environments. Whilst we would hope that other work environments do not confront that level of occupational toxicity, there is great advantage in using ORM tools as a mechanism to influence safer work behaviours within our workplaces.
-
-
- Identify the Hazards
- Ask the What If Questions
- Determine the Risk Exposure
- Implement Control Measures
-
The SAFE-T-SCAN© four (4) step process leverages the seminal influence of Operational Risk Management (ORM); a key hazard management tool of many military organizations around the World. Remember military operations are the one workplace where your competitor is out to kill/maim you. Therefore the hazard and risk management approaches, by definition, need to have the ability to function within toxic work environments. Whilst we would hope that other work environments do not confront that level of occupational toxicity, there is great advantage in using ORM tools as a mechanism to influence safer work behaviours within our workplaces.
To review the background to the SAFE-T-SOS Psycho-Behavioural Safety Systems just Click Here.
If you would like to read what the UK Health & Safety Executive says about risk assessment just Click Here.
“We develop understandings around risk long before we can walk. For many we get this wrong over and over again. Just because something bad hasn’t happened doesn’t mean we have been ‘safe’. Just because something good has happened doesn’t mean we were doing things ‘right’.”
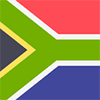
Cobus, Secunda
“David Broadbent had been assisting our company with developing a better safety culture. As part of that process we started with the SAFE-T-START & SAFE-T-SCAN processes. I had the job one day of driving David to the gate as it was end of day. When I drove back to the work site I witnessed a group of workers discussing how they would do a lift. I was surprosed to see they all had their SAFE-T-SCAN cards in their hands and appeared to be working the problem. I was very impressed and it proved to me that what were doing with David was working. Just unfortunate he was not in the car to see the magic happening.”
